Diesel Generator Preventive Maintenance Ensuring Reliable Power Supply
Introduction
In today's world, where uninterrupted power supply is critical for various industries and essential services, diesel generators play a crucial role in providing backup power during outages. These generators are relied upon to keep operations running smoothly, making preventive maintenance essential to ensure their reliability and longevity. This article will delve into the importance of preventive maintenance for diesel generators, detailing the key components and procedures involved in keeping these vital machines in optimal working condition.
Understanding Diesel Generators
Diesel generators are a common choice for backup power due to their efficiency, reliability, and robustness. They consist of a diesel engine that drives an alternator to generate electricity. When the main power supply fails, the diesel generator automatically starts up to provide electricity to critical systems and equipment. This seamless transition is essential for industries such as hospitals, data centers, manufacturing plants, and telecommunications facilities where downtime can result in significant losses.
Importance of Preventive Maintenance
Preventive maintenance is the practice of regularly inspecting, servicing, and repairing equipment to prevent breakdowns and ensure optimal performance. For diesel generators, preventive maintenance is crucial for several reasons:
1. Reliability: Regular maintenance helps identify and address potential issues before they escalate into major problems, ensuring that the generator is ready to start and operate when needed.
2. Longevity: Proper maintenance extends the lifespan of the generator, reducing the risk of premature failure and the need for costly repairs or replacements.
3. Safety: Well-maintained diesel generators are less likely to experience malfunctions that could pose safety hazards to personnel or damage equipment.
4. Cost-effectiveness: Investing in preventive maintenance is more cost-effective than dealing with emergency repairs or replacements, which can incur high costs and downtime.
Key Components of Diesel Generator Preventive Maintenance
To effectively maintain a diesel generator and ensure its reliable performance, several key components must be considered:
1. Regular Inspections: Scheduled inspections are essential to identify any signs of wear, damage, or deterioration in the generator components. Inspections should cover all critical parts, including the engine, alternator, fuel system, cooling system, exhaust system, and electrical connections.
2. Oil and Filter Changes: Regular oil changes are crucial to keep the engine lubricated and running smoothly. Dirty or degraded oil can lead to increased friction, overheating, and component wear. Filters, including oil, fuel, and air filters, should also be replaced according to the manufacturer's recommendations.
3. Fuel System Maintenance: Diesel fuel quality is vital for the proper operation of the generator. Regular fuel testing and treatment can prevent issues such as contamination, microbial growth, and fuel degradation. Fuel filters should be inspected and replaced as needed to ensure clean fuel delivery to the engine.
4. Cooling System Checks: The cooling system plays a critical role in regulating the engine temperature and preventing overheating. Regular checks of coolant levels, hoses, belts, and the radiator are necessary to maintain proper cooling efficiency and prevent engine damage.
5. Battery Maintenance: The battery is essential for starting the generator, so it is crucial to keep it charged and in good condition. Regular inspections, cleaning of terminals, and testing of battery voltage and electrolyte levels are necessary to ensure reliable starting power.
6. https://www.lkpowerplant.com : The electrical system, including wiring, connections, and control panels, should be inspected regularly to identify any loose connections, corrosion, or damaged components. Testing of voltage, current, and frequency output is essential to ensure that the generator is providing the required power.
7. Load Bank Testing: Periodic load bank testing is necessary to simulate real-world operating conditions and ensure that the generator can handle the expected load without issues. This test helps identify any performance issues and validates the generator's capacity to meet power demand.
8. Governor and Control System Checks: The governor regulates the engine speed, while the control system monitors and manages generator operation. Regular checks and calibrations of the governor and control system are essential to maintain optimal performance and synchronization with the main power supply.
9. Exhaust System Inspection: The exhaust system plays a crucial role in venting combustion gases safely away from the generator. Inspections of exhaust pipes, mufflers, and silencers should be conducted to ensure proper operation and compliance with environmental regulations.
10. Record Keeping: Maintaining detailed records of all maintenance activities, inspections, tests, and repairs is essential for tracking the generator's performance over time. Records can help identify maintenance trends, schedule future maintenance tasks, and demonstrate compliance with regulatory requirements.
Best Practices for Diesel Generator Preventive Maintenance
In addition to the key components mentioned above, following best practices can enhance the effectiveness of preventive maintenance for diesel generators:
1. Develop a Comprehensive Maintenance Schedule: Create a detailed maintenance schedule that outlines all required tasks, frequencies, and responsible personnel. This schedule should be based on the manufacturer's recommendations, industry standards, and the generator's operating conditions.
2. Conduct Regular Training: Ensure that maintenance personnel are trained and qualified to perform the required tasks safely and effectively. Training should cover proper procedures, safety protocols, equipment operation, and troubleshooting techniques.
3. Use Genuine Parts and Supplies: When replacing components or consumables, always use genuine parts and supplies recommended by the generator manufacturer. Substandard parts can compromise performance and reliability, leading to potential issues down the line.
4. Monitor Performance Metrics: Implement a system for monitoring key performance metrics, such as fuel consumption, oil quality, temperature readings, and load testing results. Tracking these metrics over time can help identify trends, anomalies, or potential issues before they impact generator performance.
5. Implement a Predictive Maintenance Program: In addition to scheduled preventive maintenance, consider implementing a predictive maintenance program that uses data analysis, condition monitoring, and predictive technologies to anticipate and address maintenance needs proactively.
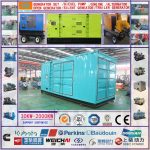
6. Collaborate with Service Providers: Establish partnerships with qualified service providers or maintenance contractors who specialize in diesel generator maintenance. These experts can offer valuable insights, technical expertise, and support for complex maintenance tasks or repairs.
7. Document Emergency Procedures: Prepare and document emergency procedures for generator failures, power outages, and other critical situations. Ensure that all personnel are trained on emergency protocols and know how to respond effectively in case of an emergency.
8. Conduct Regular Load Testing: Regularly test the generator under load conditions to verify its performance and capacity. Load testing should be performed at varying load levels to assess the generator's responsiveness, stability, and efficiency.
9. Perform Fuel Polishing: Periodic fuel polishing can help remove contaminants, water, and sediment from the diesel fuel storage tanks. Clean fuel is essential for maintaining the generator's performance and preventing fuel-related issues.
10. Review and Update Maintenance Procedures: Regularly review and update maintenance procedures based on feedback, lessons learned, and changes in operating conditions. Continuous improvement of maintenance practices can enhance the generator's reliability and performance.
Conclusion
In conclusion, diesel generators are essential assets for providing backup power in critical applications where uninterrupted electricity supply is paramount. Preventive maintenance is key to ensuring the reliable operation, longevity, and safety of diesel generators. By implementing a comprehensive maintenance program that covers all critical components, following best practices, and collaborating with qualified service providers, organizations can maximize the performance and efficiency of their diesel generators. Prioritizing preventive maintenance not only minimizes the risk of unexpected failures and downtime but also contributes to cost savings, operational continuity, and peace of mind knowing that backup power is readily available when needed.